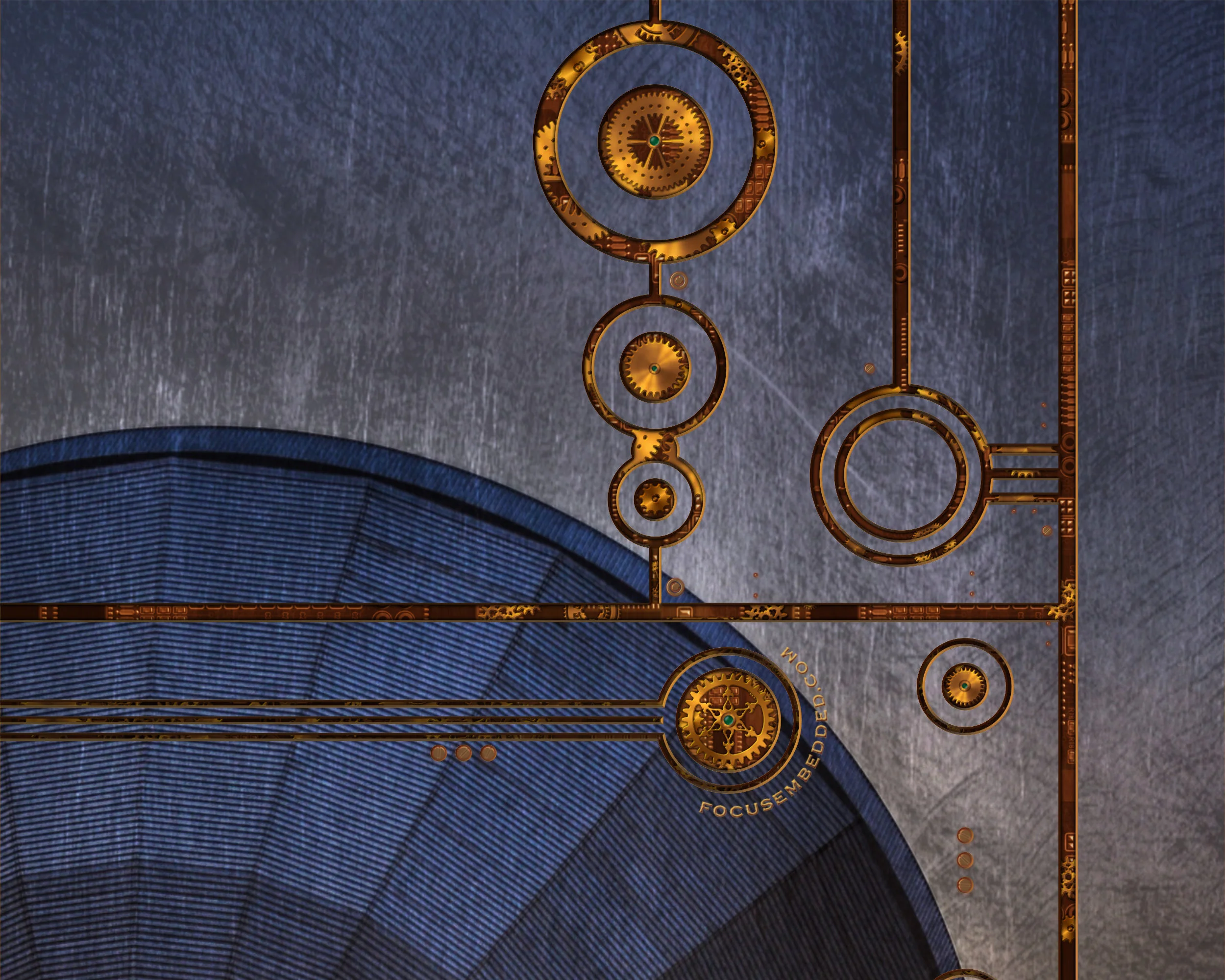
DESIGN FOR CONSUMER MARKETS
Time to market is critical.
Disruptive Technology can come from anywhere.
COGS and NRE costs have to be balanced.
Few things in the world of new product design and development are as much adrenaline-pumping fun as consumer electronics design. At Focus Embedded, we all can say we were the kids who got off the white-knuckle rollercoaster ride at the fair and ran straight to the end of the line to get back on. And with its short times to market, tight budgets, low COGS requirements, and huge payouts if you've created a winning product; much of consumer product design feels like a ride on the Coney Island Cyclone.
Frequently the very best consumer products represent a significant departure from what’s already out there in the marketplace. Or the business plan behind them is predicated on providing an extraordinary user experience that builds the kind of cult following enjoyed by companies such as Apple, GoPro, and Ferrari (who actually make more money selling Ferrari branded merchandise than they do selling cars).
When this is the situation, the engineering consulting firm that gets the nod to do product design also should be applying its creativity and innovation skills to the “optimization” problem of finding the combination of features (very well done, of course) and manufacturing components that maximize revenue in the short run while cementing brand loyalty in the long run.
The principal challenge in getting a consumer product to market (be it Audio/Video, mobile device, fitness equipment, assistive technology, IT product, or just about anything else) is that there are generally three forces at play, and just being a “tech geek” isn’t enough if you’re to balance them properly. (You’d better see engineering in its all-important economic context.)
Remember that:
Time to market is critical in the consumer space. But a desire to keep that time short is diametrically opposed to the requirement that you take the time to find the optimal solution from the point of view of “best use of technology” or “minimizing the eventual cost of goods sold.” Sometimes the best answer is to launch the “less than ideal for high volume manufacturing” product to get first mover advantage – knowing that the initial product launch is there to buy the time for the first redesign once initial adopters have provided marketing data and there’s a viable path to COGS reduction that doesn't totally miss the market window.
Often the most disruptive technologies do not come from large, established firms. True, there are firms such as 3M that are a hundred years old, have a large number of employees, and are still pushing an internal culture of innovation. But more commonly a great new product idea comes from somebody who’s left to chase it with angel or venture capital funding — meaning he may be up against some stiff budgetary limitations with some hard milestones to meet lest his backers pull out on him.
If the product eventually goes to volume, cost of goods sold – which can often only be held low with additional NRE investment – will become critical. Then again, with a high-volume product NRE costs are much more easily amortized, and it can be well worth it to spend $10,000 now for design work that’ll get $1 out of every one of those 100,000 units you’re likely to sell over the next year or two. Again, there’s an economic balance to be struck.
What should be obvious about consumer product development strategy is that perhaps more than any with any other kind of design activity, any engineering consulting firm you have helping you had better have a firm handle on not just the technology but also the economic model that makes the product viable in the market space to begin with. There’s a whole lot more to it than just hardware design, software design, chip design, or circuit board layout being done in a financial vacuum.
Focus Embedded is home to an unusual breed of engineers who can solve the very hardest of technical problems without losing track of the underlying economic reasons why they’re worth solving. We’re not just going to take a specification and implement it without being very sure we understand our customer’s point of view and what drove the spec to look like it does in the first place.
At Focus Embedded, it’s our job to be sure you know what can be done, outline how it can be done, and suggest viable alternatives that might fit your business model better -- because no market demands this of an entrepreneur the way the consumer market does.
And then we do the part where we implement the technology better than anybody.

INSTRUMENTATION DESIGN
Instrumentation amplifiers, which are analog circuits, are your window to the world. Do one poorly, and you'll be looking through a fogged window.
Properly characterizing what you're measuring is critical to getting your analog front end and data collection system defined correctly.
Signals can be filtered with an analog front end or manipulated later in software. Knowing where to do one or the other depends on a solid knowledge of both analog and digital signal processing theory.
Without correctly designed instrumentation circuitry, the smartest embedded microprocessors and microcontrollers on the planet would never have a window into the very real (and complex) analog world in which we all live.
Whether it’s a biometric device for a security application, an extremely low-noise amplifier for a photomultiplier tube that measures light by counting individual photons, or an electroencephalogram looking at the millionth of a volt required to fire a neuron; getting the measurement taken accurately – before it’s digitized and operated on by an embedded processor – can mean the difference between having the information to complete a critical calculation correctly and having a buffer full of bad data.
Obviously biological reactions are one place where bandwidth requirements can be very low but electronic noise in the instrument itself can quickly swamp the actual measured signal. So keeping analog and digital electronics separate from each other is critical, and proper printed circuit board layout can easily mean the difference between success and failure. But even in the world of medical equipment design, the difference between a correct diagnosis and a poor one may be the availability of a few data points resolved to higher granularity – so there’s no guarantee the process of new product design and development won’t also involve the balancing of bandwidth (in order to get enough readings taken within a period of time) and the absolute accuracy of a single measurement. Certainly this is true of medical imaging, where pixels come out of imager modules at blinding speeds while also demanding accuracy out to one part in ten thousand.
In short, having a properly designed analog front end is critical to being able to make the most of all of the mathematical tools (Discrete Fourier Transforms, Fast Fourier Transforms, digital filtering, general DSP algorithms, Laplace Transforms, Poisson Statistics, Root Locus of Evans and Routh-Hurwitz for stability, etc.) at your disposal. Knowledge of digital signal processing (and what can and can’t be done on the back end) will inform the specifications of the analog circuits that interface with the world beyond the printed circuit board. And sometimes, with remote telemetry systems, knowledge of how the communications channel works – again a signal processing question – will determine how the captured data from the instrumentation system is packed (and perhaps compressed) before being sent on.
When you need instrumentation (or telemetry systems) designed properly, you need the design engineering services of a company that can design across the analog and digital domains as well as do the “heavy math” to determine what data should be taken and how it should be sorted.
If you need instrumentation designed, you need Focus Embedded.

MEDICAL DESIGN
If you don't have an audit trail for your medical design, you may as well not bother doing it. Inadequate documentation is reason enough for the FDA to make you go back and do everything over.
Biological signals are usually low frequency and low amplitude. Knowing how to trade bandwidth for accuracy is often critical to making medical devices work.
If your medical system requires any kind of feedback control, "hacking code" to make a control loop work is a cardinal sin. You have to have modeled device behavior thoroughly or you will have set yourself up for FDA rejection at best and a class-action lawsuit or mass tort at worst.
There are any number of medical product development companies out there. And there are similarly plenty of engineering consulting companies offering electronic design services. But if you’re planning on eventually making any money in the medical devices market, you’re going to have to jump through the hoops that say you’re compliant with HIPAA regulations and that you can pass the scrutiny of the FDA for acceptance into clinical trials or the issuing of a 501(k) clearance. And your product design company is going to have to make those jumps with you.
Here is where unless you’re planning on taking a few small steps forward followed immediately by a few more giant ones in a backwards direction, you’d better be partnering with medical device design consultants who have strict audit trails for every piece of work they do – be it for medical equipment or assistive technology design, or be it for simply a consumer or entertainment product. And we at Focus Embedded figured out a long time ago that the best way to design things (for all markets, medical or otherwise) is to be able to document the design process at every step and quickly ferret out any potential mistakes before they propagate.
Mind you, this discipline helps you at both ends of the medical design cycle, since not only do you not have to face the problem where the FDA makes you redo much of your work to correct the lack of an auditable process, you also don’t have nearly as much trouble convincing your own suppliers to certify their components for use in medical markets. (Because of liability issues, many of them won’t do this – particularly if the end product is used for life support – unless they’re very sure that the people buying their stuff aren’t throwing it together haphazardly.)
Engineers at Focus Embedded have been doing design of analog instrumentation amplifiers for medical/biological systems since back in the days when A-to-D converter offerings were few, far between, and very expensive. So we’ve mastered analog circuit design to a degree few others have (at least in the last 30 years, anyway). At the same time, we have on staff several designers whose work over the years has been on the cutting edge of the kind of DSP-based compression techniques used in medical imaging. And we’ve done our share of spatial Fourier transform wavelet engine design for medical systems.
Even in technology areas as seemingly mundane as low-power switching power supply design, when you’re working with anything that might touch a patient, even indirectly, it pays to work with people who are building in safety and an audit trail from the beginning.
It pays to work with Focus Embedded.

INDUSTRIAL & CONTROLS DESIGN
Several highly complex forms of mathematics have evolved to describe feedback control.
A high percentage of people who attempt to design control systems have no idea that the math that describes them even exists - and they therefore can't predict whether they'll be stable or have acceptable transient response.
The more complex a software controls algorithm is, the less deterministic its time to completion becomes. For this reason, a complex software control loop can have enough jitter in it to cause a system instability somewhere else.
Sometimes mild system instability is actually desirable. But you have to know when - and how far you can push into the right half of the s-plane before you have a problem.
Control systems design seems to be the one place in the world of new product design and development where more people want to fly by the seats of their pants than any other. And because control systems theory says (quite clearly) that there are limitless ways in which minor changes in the real world can move poles in the complex plane, it’s no wonder so many people unwittingly create systems with poor transient response at best and unanticipated system instability at worst.
That RS422, RS432, RS485, I2C, Ethernet - TCP/IP, IP Ethernet, CAN, or Fieldbus data link between your plant and your plant controller has some latency. Do you know what it is and how that’s introducing a phase delay into everything you eventually do to control the plant? And have you figured out where the feedback loops should go and what their influence should be? Will you need some kind of estimator to make it all stable?
In layman’s terms, if you buy a bunch of sausages and let them sit for a day under refrigeration before you cook them, the spices mix with the meat, and they’re tastier. But let them sit for a month and see what happens when you eat them. And by the way, do you want to eat them when the best anybody can say to you is that they’ve been in the refrigerator for some amount of time between a day and a month?
Proper observation of the rules of linear time invariance (LTI) theory and a knowledge of the advanced mathematical techniques for predicting system stability (Root Locus of Evans, Routh-Hurwitz Matrices, etc.) can make the difference between a system performing optimally and one being overdamped, underdamped, or flat-out unstable. In extreme cases you may find that instability is actually a desirable thing so long as the controlled system doesn’t spend too much time in an unstable operating regime, since it’s instability that actually goes hand-in-hand with fast transient response.
(The Wright Brothers recognized that their 1903 Flyer was inherently unstable, but they concentrated their efforts on the directional controls problem that would allow the pilot to correct its behavior. Samuel Langley chose to try to make his Aerodrome stable and then focused all his efforts on making a more powerful engine. And in the end, the Flyer lifted off from the sands of eastern North Carolina and the Aerodrome went straight from its launcher on top of a houseboat to the bottom of the Potomac River.)
Whether your problem is servo control, motor control, some complex chemical process control, or any of a million different challenges in the area of feedback control of a dynamic system; you owe it to yourself to find the people who are going to solve the theoretical half of your problem first and then immerse themselves in the practical problem of reducing it to real-world circuits or software. Diving in and whipping out circuits without knowing the mathematical underpinnings of what they do is a formula for trouble.
And at Focus Embedded, we bother to read the pull date on the sausages before advising that anyone eat them.

GOVERNMENT, AEROSPACE & DEFENSE
When you're 11 miles high, moving 19 miles a minute, reliability counts.
Predictability and repeatability matter enormously in military and aerospace applications, since in few other places is the cost of being wrong so high.
In military and aerospace applications, hostile environments are frequently part of the engineering system and need to be modeled as such from the beginning.
You can't design in reliability after the fact in 99.9% of all cases.
At a speed of Mach 1.6 and an altitude of 60,000 feet AGL, “Abort, Retry, Fail?” doesn’t cut it. And when an enemy missile is incoming, nobody wants to see the message, “A system error has occurred. Okay?”
No, it’s not okay.
Focus Embedded lives (and thrives) in the very demanding world of embedded electronics – where deadlines can be quite hard and the penalties for missing them absolutely fatal – for the reason that we never “abstract away” a fundamental problem until we’re sure we’ve mastered it at its lowest level. Whether it’s designing an FPGA, working through an exercise in signals intelligence (SIGINT), figuring the best way to implement avionics or biometrics, reducing a Discrete Fourier Transform (DFT) to practice or otherwise developing a Digital Signal Processing (DSP) algorithm, coming up with a telemetry system, or readying our troops for electronic warfare; Focus Embedded understands the importance of identifying what the system on the drawing board has to do in the real world. We’re not a middleman in the business of subcontracting. This is where the buck stops. We’re the guys who really do the work.
We’ve tackled the design of everything from switchmode power supplies for VME chassis’ to advanced high speed data acquisition systems for high-resolution remote video to VITA-57 mezzanine cards for advanced FPGA prototyping systems. Whether it’s SATCOM and it’s somewhere in orbit, it’s on a NASA probe and it’s millions of miles from earth, it’s sonar and it’s somewhere under the oceans, or it’s the controller for a tank transmission and it’s in the most hostile environment you can find right here on terra firma; we’ve probably worked on it or something like it.
When you can’t leave anything to chance, you owe it to yourself to drop us a line and tell us about your design requirements. Before you’re done looking over our offerings, we’re pretty sure you’ll agree that if it requires mission-critical electronics, it requires a Focused effort.